Researchers experiment with 3000 times gravitational acceleration
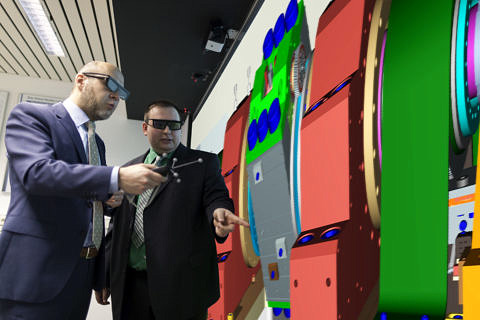
FAU and Schaeffler develop new high-performance test stand
FAU researchers will test rolling bearings under extreme conditions of 3000 times gravitational acceleration and the corresponding high loads. For this purpose, FAU’s Chair of Engineering Design has developed a unique rolling bearing spin test stand (Wälzschleuderprüfstand, WSP) together with Schaeffler in order to investigate the behaviour of the bearings’ material and design more closely. The results of this research project will be used to optimise current rolling bearing technology and reduce the fuel and energy consumption of vehicles and machines.
Rolling bearings: a tried and tested component made in Franconia
Rolling bearings can be found everywhere in industry and day-to-day life. Without them, wheels cannot turn, motors cannot run and gearboxes cannot function. They consist of an inner and an outer ring with the rolling elements arranged between them. The axis of a wheel, for instance, is surrounded by the inner ring and exerts load on the rolling elements from there. It is assumed that the principle of such bearings was already known to the Romans and was eventually fully developed by Leonardo da Vinci in the 15th century.
Northern Bavaria is the centre of the European rolling bearing industry
When the ball mill was invented in Schweinfurt in the late 19th century, it was possible to produce specific ball bearings on an industrial scale for the first time. This was the beginning of the European rolling bearing industry, which still has its centre in Northern Bavaria. The majority of bearings tested by FAU’s Chair of Engineering Design on the WSP are needle roller bearings in which cylindrical rollers are arranged between the rings. In relation to their diameter these cylindrical rollers are rather long. They are used in automotive transmissions, for example.
Test stand weighing several tons
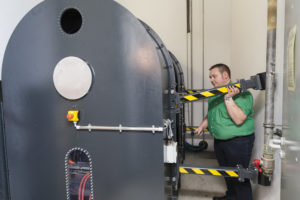
Only little research has yet been conducted into the friction behaviour of rolling bearings under high centrifugal forces such as those produced on the WSP. Together with Schaeffler, FAU’s Chair of Engineering Design has developed a new test procedure to investigate the extreme loads exerted on the material and design. The questions arising in this context are to be addressed in experiments and simulations.
‘With this test stand, we will be able to gain a better understanding of the phenomena associated with rolling bearings in the centrifugal force field. In this context, it is important for us to refine our simulation tools for rolling bearings based on the test results. This will help us translate the findings into application-orientated conditions and further improve our product development,’ states Oliver Graf-Goller, project co-ordinator at Schaeffler, with regard to the test stand’s significance.
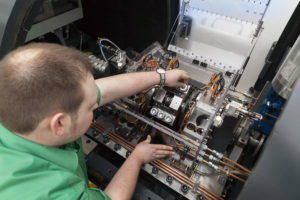
‘Lightweight design and energy efficiency are two key factors in the development of new vehicle components. Improvements are directly visible in reduced fuel consumption,’ explains Dr. Stephan Tremmel from the Chair of Engineering Design. ‘On our test stand, we can investigate, in particular, the question of which factors influence the bearings under extreme load. Such factors may be temperatures, coatings or geometric details.’
Approximately 400 times the load experienced by a fighter pilot
Together with Schaeffler, the researchers developed a test stand on which the bearings are exposed to 3000 times gravitational acceleration. This corresponds to approximately 400 times the load fighter pilots are exposed to.
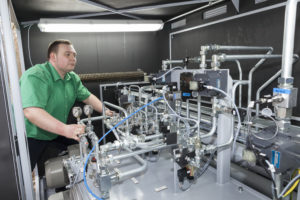
‘The bearings rotate twice. Just like the planets in our solar system, they rotate around their own axis and all of them together rotate around the central axis using an open planetary gear,’ says David Hochrein, Dr. Tremmel’s colleague, providing an explanation of the underlying principle.
The FAU researcher developed the entire test stand, which weighs 16 tons and is located in its own 22 square metre test bunker, and built it together with his colleagues from the Faculty of Engineering’s central mechanical and electronics workshop.
Test stand and computer simulation
The project, which costs around 800,000 euros, also has another purpose. In collaboration with their partners at Schaeffler, the researchers refined and improved the software which is required for essential simulation procedures. This software is used to simulate the rolling bearings’ behaviour and optimise it in the computer model even before the prototype is built. ‘Therefore, the WSP, which is a completely new development in the field, is also used to verify the calculations and virtual models. Eventually, the test stand and the improved computer models will help us gain a much better understanding of the rolling bearings’ friction behaviour under extreme conditions,’ says Prof. Dr. Sandro Wartzack, head of the Chair of Engineering Design, regarding the purpose of the joint project.
Further information:
Dr. Stephan Tremmel
Phone: +49 9131 8523222
tremmel@mfk.fau.de