Using digital systems to reduce cable clutter for on-board networks in vehicles
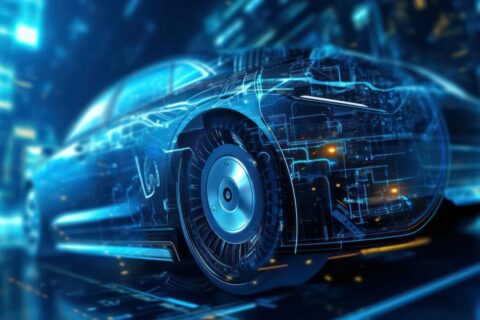
Research project at FAPS at FAU wants to return manufacturing to Germany
Vehicle on-board networks have played a central role ever since the introduction of electric cars. The cable clutter in each car represents the increase in electrification of vehicles which will one day enable autonomous driving with safety-critical functions. This will finally transform on-board networks into the nervous system of mobility. Currently, manufacturing processes for these wiring harnesses require large numbers of personnel and are not highly automated.
As part of the “Next2OEM” project funded by the Federal Ministry for Economics Affairs and Climate Action, researchers at FAU now want to examine, digitalize and automate the entire value chain. This will eliminate both the “clutter” of steps in the process and in the responsibilities involved. At the end of the project carried out by the Institute for Factory Automation and Production Systems (FAPS), a prototype will be produced that will ensure on-board networks are “Made in Germany” once again. The Next2OEM project has an overall volume of over 24 million euros and is scheduled for completion in January 2026.
Complex nerve pathways in on-board networks
For drivers, on-board networks are a type of black box as they are practically invisible. However, these customer-specific wiring harnesses form a complex “nerve system” in a vehicle. Even a medium-sized passenger car contains an average of around 3000 individual cables that, along with other components in the on-board network, come to a total weight of 55 kilos.
In the past, the value chain simply grew with the product and process structures without rethinking it. For example, priority was given to cost efficiency which led to excessive logistics. Due to the cheaper costs involved, North Africa and Ukraine have become established manufacturing locations. In some cases, this can mean that cables and smaller components are shipped back and forth across the globe before ending up in Germany for final assembly at an original equipment manufacturer (OEM). The Russian invasion of Ukraine made the lack of resilience of these supply chains obvious and, during the coronavirus pandemic in particular, the fragility of procurement processes became apparent.
FAPS and project partners examine entire value chain
To enable reshoring of wiring harness manufacturing to Germany in future, FAPS and the Next2OEM partners are developing something known as a graph-based information model. This model is based on digital data and how they are exchanged for each product and every manufacturing and transport process. This digital ecosystem facilitates the newly-developed manufacturing processes in Next2OEM. The aim is to implement automated wiring harness manufacturing and installation at OEMs. The Next2OEM project will result in a demonstration system for highly-automated wiring harness manufacturing in a vehicle.
This will include, for example, solutions to manage the handling of components and cables with unstable forms. In addition, it will ensure traceability back to the component and process level for the first time. Furthermore, in terms of the impact on the environment, it will shorten logistics routes and thus reduce the CO2 footprint. Data will become available about which components were installed and checked when and where and the size of a product’s CO2 footprint virtually at the touch of a button.
All partners at one table
The consortium comprises partners from the entire value chain including everything from plug-in connector manufacturing and cable assembly, shaping, cable protection, testing and logistics to the assembly of the wiring harness into the car body. Consortium leader AUDI AG is responsible for testing and validating the feasibility of the prototype of the entire system.
The project partners are TE Connectivity and KOSTAL Kontakt Systeme as connector manufacturers, semantic PDM for the development of the graph-based information model, and Kromberg and Schubert as wiring harness manufacturers. Other important partners in automation include Komax Taping, Komax Testing, Stefani Maschinenbau, BÄR Automation and ArtiMinds Robotics.
Further information:
Huong Nguyen
Institute for Factory Automation and Production Systems
Phone: +49 911 5302 99115
huong.nguyen@faps.fau.de